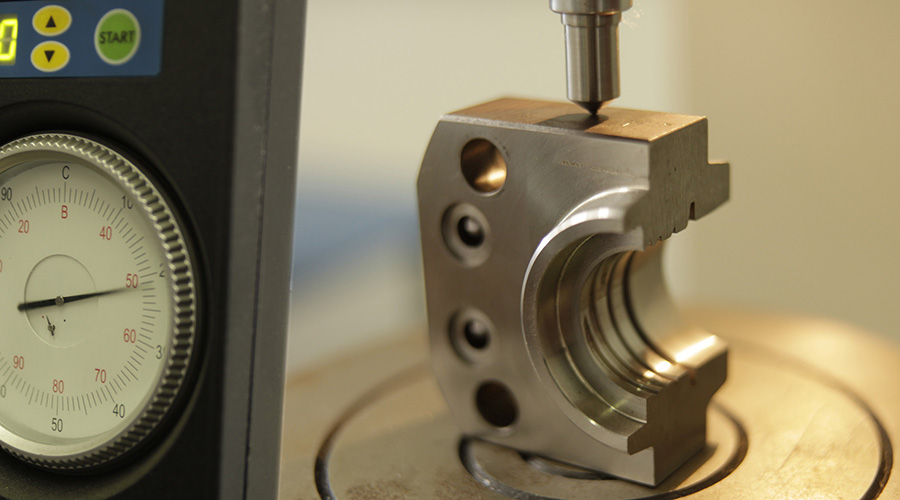
LEIZHEN Mold Company: Step-by-Step PET Preform Mold Design Process
At LEIZHEN Mold Company, we combine innovation, precision engineering, and decades of expertise to deliver high-performance PET preform molds for global clients. Our streamlined design process ensures optimal functionality, durability, and compatibility with blow-molding systems. Here’s how we craft molds that meet your exact needs:
1. Requirement Analysis & Concept Development
Client Consultation: Collaborate with customers to understand bottle specifications (neck diameter, capacity, thread design), material (PET resin grades), and production goals (cycle time, cavity count).
Market Research: Analyze industry trends (e.g., lightweighting, sustainability) to align designs with market demands.
Feasibility Study: Evaluate mold complexity, cost, and timeline using advanced CAD software.
2. 3D Modeling & Simulation
CAD Design: Create detailed 3D models of the preform mold, optimizing gate placement, cooling channels, and cavity layout for uniform material distribution.
Mold Flow Analysis: Simulate injection molding processes to predict flow patterns, minimize warpage, and reduce cycle times.
Stress Testing: Validate designs for durability under high-pressure conditions using FEA (Finite Element Analysis).
3. Material Selection & Prototyping
High-Grade Materials: Choose hardened steel (e.g., H13, Stainless Steel 420) or specialty alloys for corrosion resistance and extended mold lifespan.
Rapid Prototyping: Develop a functional prototype for testing preform weight, wall thickness, and compatibility with blow-molding machines (e.g., SIPA, Husky).
Client Feedback: Refine designs based on prototype performance and customer input.
4. Precision CNC Machining
Cavity & Core Fabrication: Use 5-axis CNC machining to achieve micron-level accuracy (±0.01mm) in critical components.
Surface Treatment: Apply polishing, nitriding, or chrome plating to enhance wear resistance and reduce friction during injection.
Assembly: Integrate ejector systems, cooling lines, and hot runner systems (if required) for seamless operation.
5. Rigorous Quality Testing
Dimensional Inspection: Verify preform dimensions (neck finish, body thickness) using CMM (Coordinate Measuring Machines).
Cycle Testing: Run 500+ cycles to assess mold performance under high-speed production conditions.
Compliance Checks: Ensure molds meet FDA, EU, and ISO standards for food safety and recyclability.
6. Production & Delivery
Mass Production: Scale up with multi-cavity molds (4-144 cavities) for high-volume output.
Packaging & Logistics: Safeguard molds with anti-rust coatings and deliver globally via air or sea freight.
After-Sales Support: Provide maintenance guides, troubleshooting, and technical assistance.
Why LEIZHEN Excels in PET Preform Mold Design?
✅ End-to-End Customization: From concept to production, tailored to your brand.
✅ Fast Turnaround: 20-30 days for standard molds.
✅ Energy-Efficient Designs: Reduce scrap rates and energy consumption.
✅ 24/7 Technical Support: Ensure uninterrupted production.
Transform Your Bottle Manufacturing Today!
Partner with LEIZHEN Mold Company for innovative PET preform molds that ensure precision, speed, and scalability. Contact us for a free quote or design consultation!