High Quality 16 Cavity Preform Mold PET Bottle Making
This 16-cavity preform mould is used to produce preform, which can be used to produce water bottles, baby bottles, cosmetic bottles, sauce bottles, and so on through the bottle blowing process.
Our moulds are made entirely of S136 steel. S136 is a plastic mould steel with excellent production characteristics, which has corroision resistance, polishing resistance, wear resistance, machinability, and excellent stability, and excellent stability during quenching.
Our anvantages
| High quality |
Reasonable price | |
Strict delivery time | |
Good after-sales service | |
Profession maker for 10 years | |
Gold supplier 7th year | |
Strict quality control | |
professional injection mould | |
3D design |
1. All templates are pre hardened, and the template material is 4CR13.Mould parts(core, cavity, lip etc.) materials are S136 high strength anticorrosive steel,hardness is higher than 48HRC
2. High quality hot runner parts, specialized balanced hot runner system. Special hot runner for mould ensures the same pressure and PET flow ratio of each cavity, decreases the wall thickness difference, eccentricity and AA value
3. The international first-class finishing equipment (GF Shamir EDM, America Haas, Beijing carved machine, Caisi 3 coordinate detector, etc.) to ensure the strict requirement of product size, high accuracy and interchangeability of cavity parts.
Number of cavity | 4, 8,12,16,24,32,48,64,72,96 |
Neck size | PCO28, ALCOA1716, BPF-C, ISBT1881 , 30/25, 2925,1810 etc |
Material | 4CR13 & S136 |
Hot Runner | Nozzles without heat insulation cap |
Cooling water tube | 1 inch / 2 inch |
Hardness | Up to 48HRC |
Plastic type | PET/PP |
Application machine | Husky/Unique/Chen Hsong/Yizumi/Powerjet etc |
Leizhen’s Advantages in the Preform Mold Process: Precision, Innovation, and Reliability
In the competitive world of PET preform mold manufacturing, Leizhen has emerged as a trusted partner for brands and bottlers worldwide. Renowned for its engineering expertise, cutting-edge technology, and customer-centric approach, Leizhen delivers molds that optimize production efficiency, quality, and cost-effectiveness. Here’s an in-depth look at the advantages that set Leizhen apart in the preform mold industry:
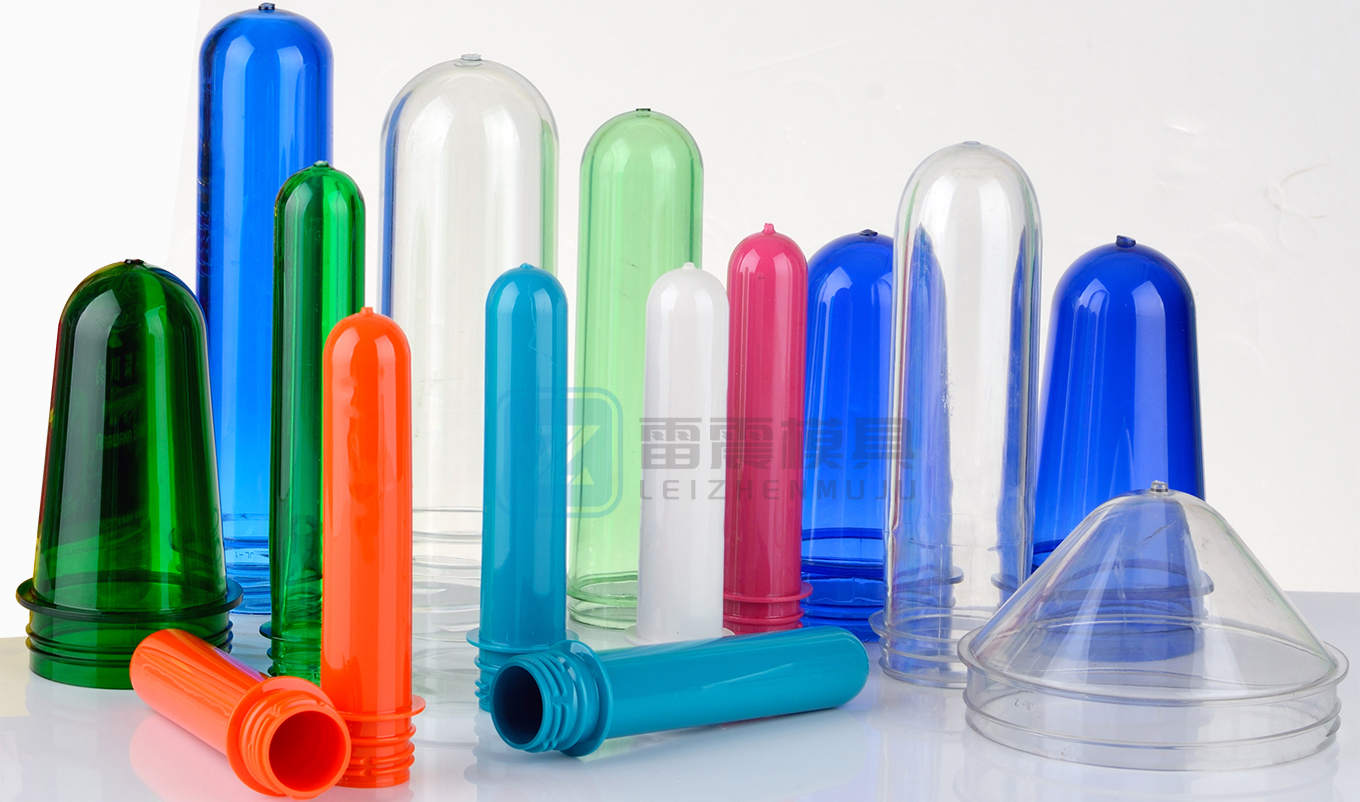
Professional PET preform mold manufacturer | Helping efficient production and achieving perfect bottle shape
As an industry-leading PET preform mold manufacturer, we focus on providing high-precision, long-life, customized preform mold solutions for global beverage, food, daily chemical and pharmaceutical companies. From design to mass production, we use innovative technology and excellent quality to help you achieve a double breakthrough in production efficiency and product quality!
(Mold Cav Qty) | Neck Size) | Application |
18 cav | 48mm, 38mm,30/25,20/25, PCO1881, PCO1810 | Water, Juice, CSD, Daily chemical products, edible oil, medicine |
24 cav | 48mm,38mm,30/25,29/25, PCO1881, PCO1810 | Water, Juice, CSD, Daily chemical, products, edible oil, medicine |
32 cav | 48mm,38mm,30/25,29/25, PCO1881, PCO1810 | Water, Juice, CSD, Daily chemical products, edible oil, medicine |
48 cav | 48mm,38mm,30/25,29/25, PCO1881, PCO1810 | Water, Juice, CSD, Daily chemical products, edible oil, medicine |
56 cav | 48mm, 38mm, 30/25, 29/25, PCO1881, PCO1810 | Water, Juice, CSD, Daily chemical products, edible oil, medicine |
72 cav | 38mm, 30/25,29/25, PCO1881, PCO1810 | Water, Juice, CSD, Daily chemical products, medicine |
96 cav | 38mm, 30/25, 29/25, PCO1881, PCO1810 | Water, Juice, CSD, Daily chemical products, medicine |
112 cav | 30/25, 29/25, PCO1881, PCO1810 | Water, Juice, CSD, Daily chemical products, edible oil, medicine |
128 cav | 30/25, 29/25, PCO1881, PCO1810 | Water, Juice, CSD, Daily chemical products, edible oil, medicine |
144 cav | 30/25, 29/25, PCO1881, PCO1810 | Water, Juice, CSD, Daily chemical products, edible oil, medicine |
176 cav | 30/25, 29/25, PCO1881, PCO1810 | Water, Juice, CSD, Daily chemical products, edible oil, medicine |
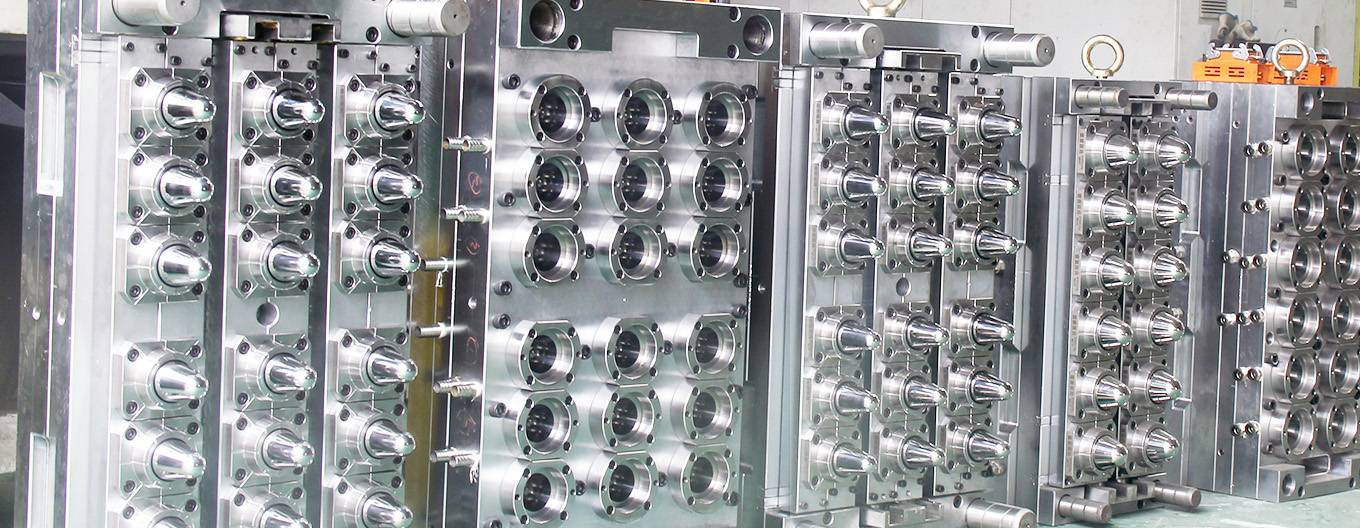
Uniform Preform Quality: Advanced flow simulation software balances the runner system, guaranteeing consistent filling and wall thickness across all cavities.
Tight Tolerances: Precision machining (±0.005mm) ensures compliance with international standards (e.g., PCO 1881, BPF) for neck finishes and thread designs.
Durability: Molds are crafted from premium steel (H13, S136, or 420 stainless steel) with heat treatment (HRC 48–52) to withstand millions of cycles.
Conformal Cooling Channels: 3D-printed or machined cooling channels follow the contour of the preform, reducing cycle times by up to 30% and minimizing warpage.
Hot Runner Systems: Partnerships with top brands like Yudo or INCOE ensure leak-free, energy-efficient melt delivery. Valve-gated systems enable clean gate cuts for lightweight preforms.
High-Speed Compatibility: Molds are optimized for machines with clamping forces up to 1,500 tons, achieving cycle times as low as 8–12 seconds for 20g preforms.
In-House Testing: Every mold undergoes trial runs on injection molding machines to validate cycle times, cooling efficiency, and preform dimensions.
ISO Certification: Compliance with ISO 9001 standards ensures traceability and accountability at every production stage.
Third-Party Inspections: Collaborations with global certification bodies verify compliance with FDA, EU, and other regional regulations for food-grade PET.
Competitive Pricing: Direct manufacturing in China reduces overhead costs, offering savings of 20–40% compared to Western suppliers.
Long Mold Lifespan: Durable materials and coatings (e.g., nitriding, DLC) extend mold life to 3+ million shots, lowering cost-per-preform.

How to place an order for moulds? | |
1.R&D | We support customer R&D. Make the files or improve the design if you needed. |
2. Quotation Making | Mould Quotation will be finished in 1 day according to the information we get. |
3. Negotiation | The quality, price, material, delivery time, payment item, etc. |
4. Mould Design | 1-2days for product 3D/2D drawing design as per customer's design. Then in further make the mould 2D/3D design. |
5. Mould | 1. confirm the products and the mold design |
2. Mould material prepare | |
3. Rough machining(heat treatment on mold base and pre-harden on mold) | |
4. CNC/ Vacuum Hardening on mold main spare parts | |
5. finishing machining( JDPAINT, DEM.etc) | |
6. Dimension inspection | |
7. Ejector& runner& cooling & other device processes | |
8. Assemble mold | |
6. Mould Testing | When moulds are finished, we will test the mould and we will send samples to client. |
7. Sample confirmation | If the first sample is not satisfied by the customer when it is come out. We modify the mould until meet the customer’s satisfaction. |
8. Delivery | Delivery goods by sea or by air, according to customer’s requirement. |